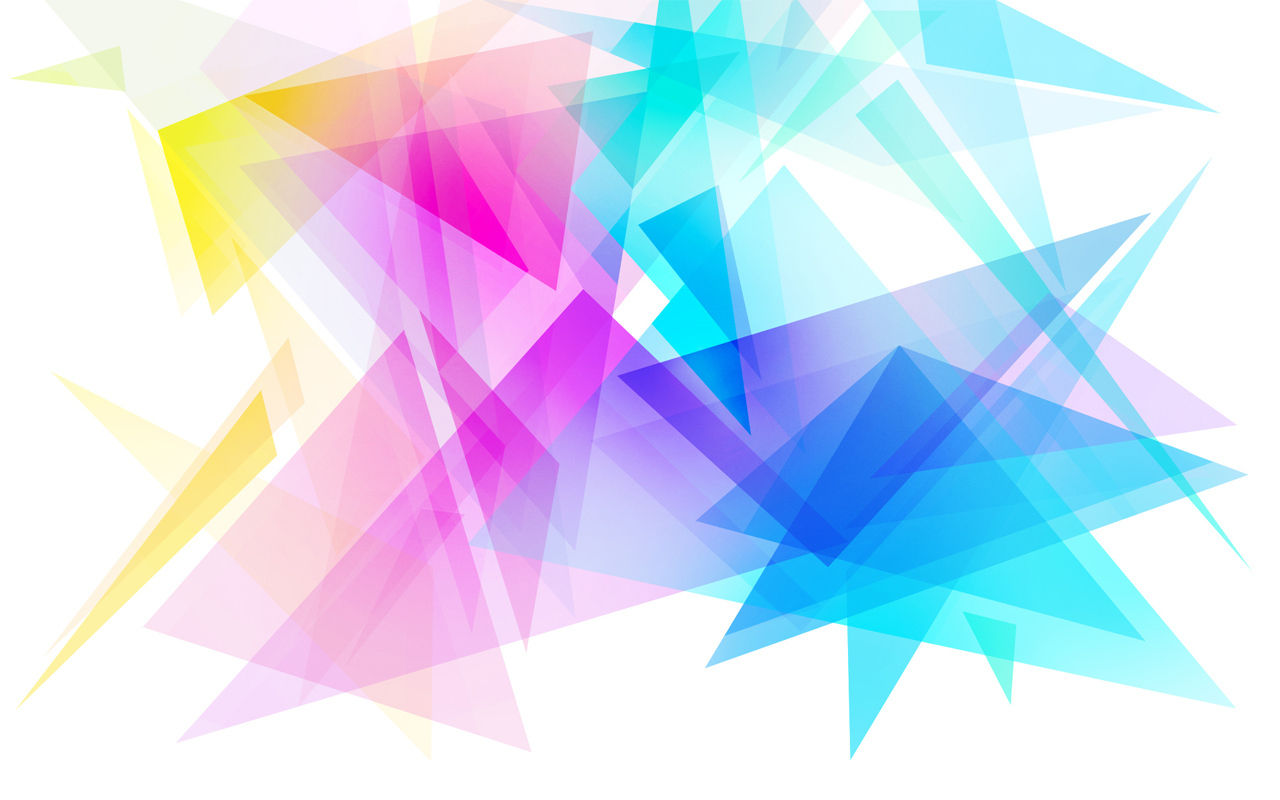
Images of Light Jewelry
Designs by
Dorthy Kneisel
The making of a piece of wearable art~
I begin by cutting shapes from different color and patterns of glass
and arrange them on top of the shape I want the pendant to be.
Once I a have placed the pieces and I am satisfied with the design,
it is fired in a kiln to 1200 degrees. This fuses the pieces together.
Then it takes on a life of its own. No two pieces are ever alike.
I will fire some pieces twice or more, depends on what design
I am going for.
It takes about 2 hours for the kiln to reach 1200 degrees. Once it
reaches that desired temperature, I turn the kiln off and the pieces must cool down completely before I can see them. This is the most exciting time for me. I am never sure exactly what colors will dominate.
The properties in the manufacturing of Dichroic glass cause the colors to change and shift once it is fired. The look takes on the shimmer and iridescence of butterfly wings and no two pieces will ever come out alike.
Sometimes I wrap the completed pendant in silver silver wire to add even more to the design, or sometimes the design looks beautiful by itself.
My name is Dorthy and I love working with Glass,
from stained glass to hot glass.

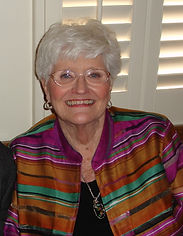